Activity Details

Type: Toolsheet
Functions​
• Display of all details of single activities
• Find patterns of correlating events
• Find patterns of the selected activities on the timeline
• Detect direct impact of the activity on the lead time of the process
• Identify activities that are linked with the occurrence of the selected activity
• Identify the process context that is linked with the activities
Benefits​
Save time and money as well as increase employee and customer satisfaction by doing the following:
• Identify potentials to reduce unwanted activities
• Identify potentials to stabilize the process lead times
Getting here​
The Activity Details Sheet is available in the list of Sheets from the Sheets tab on the Template App. When you first open it, no activity is selected, so there will be no data in the visualizations. You will have to select a specific Activity to analyze.
Alternatively, if you click on any node in the Process Analyzer, the node popup window will appear. At the bottom on the rigth side of said window is a link that will take you the the Activity Details sheet with this particular selection.
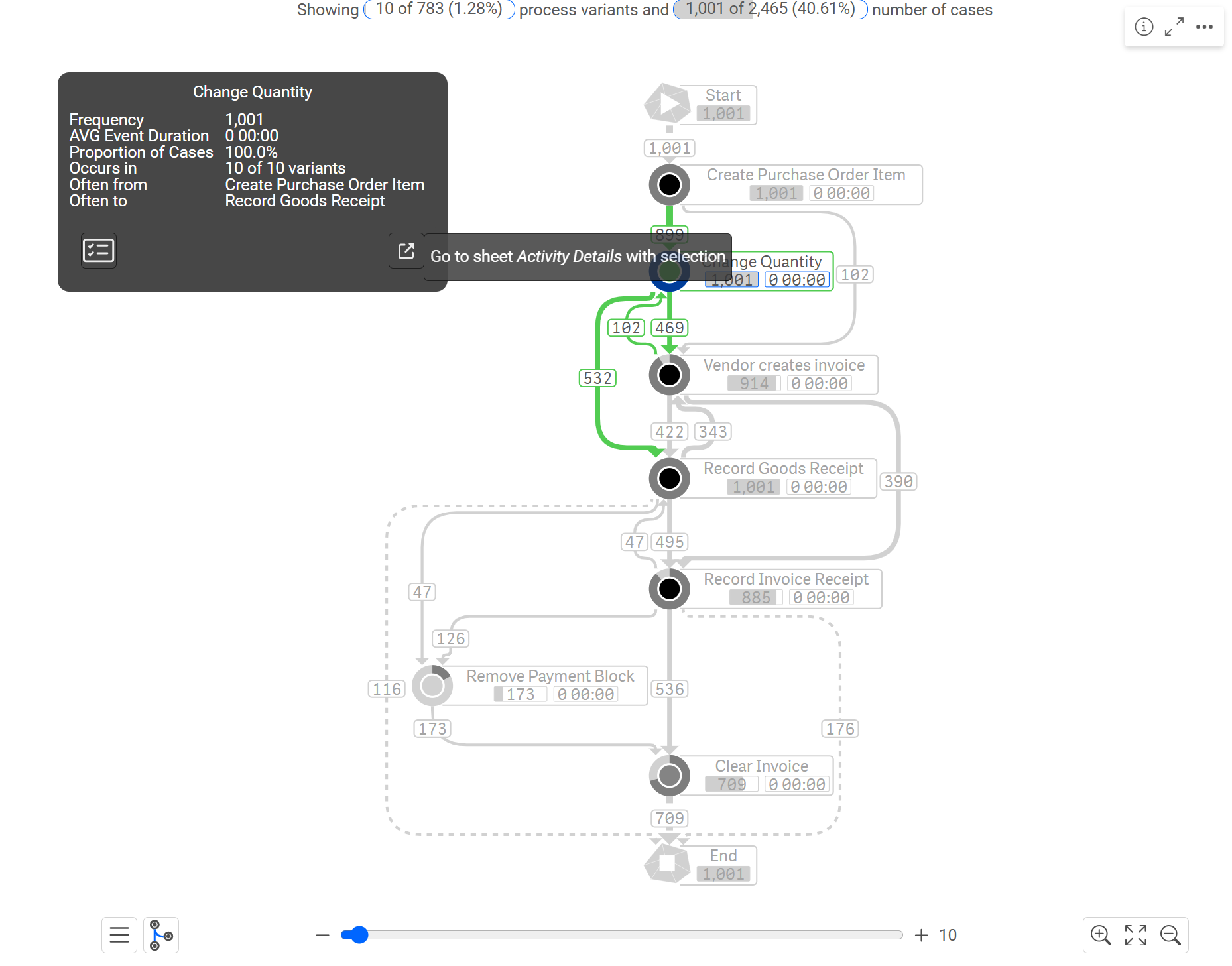
Interpreting the Visualizations​
Key Figures​
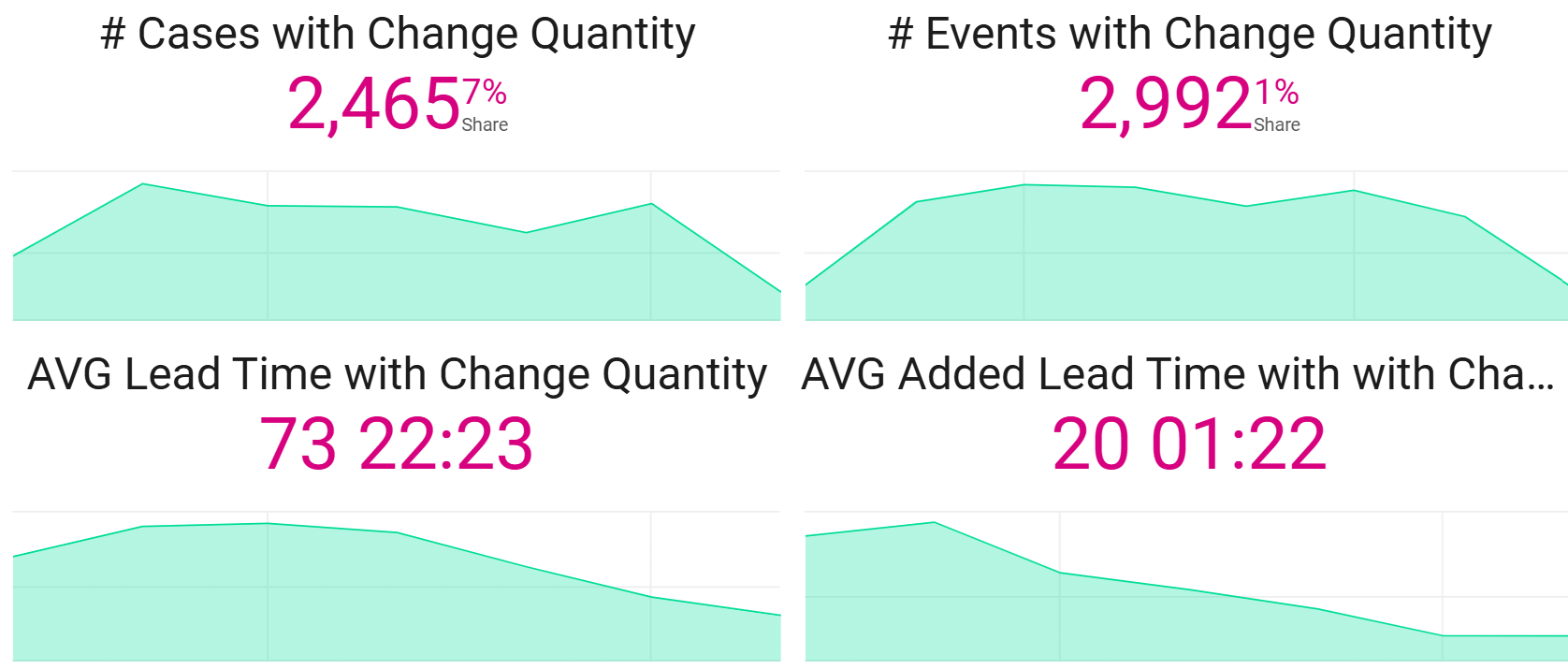
At the top left you will see four key figures and underneath their numbers a timeline showing how they have changed over time, so you can quickly see whether the numbers are improving or getting worse. You can also quickly see patterns, like a spike or drop in number at regular intervals (quarters or months, for instance).
# Number of Cases with Change Activity​
- Shows the number of cases with this particular change activity. Change events usually indicate rework, so the ideal situation would have a low number.
# Events with Change Activity​
- Ideally, this number would be low.
Average Lead Time with Change Event​
- This indicates the average amount of lead time in all cases with this Activity. This figure should be low.
Average Added Lead Time with Change Event​
- This indicates the average amount of extra (added) lead time in cases with this Activity as compared to those without it. This figure should be low.
Table​
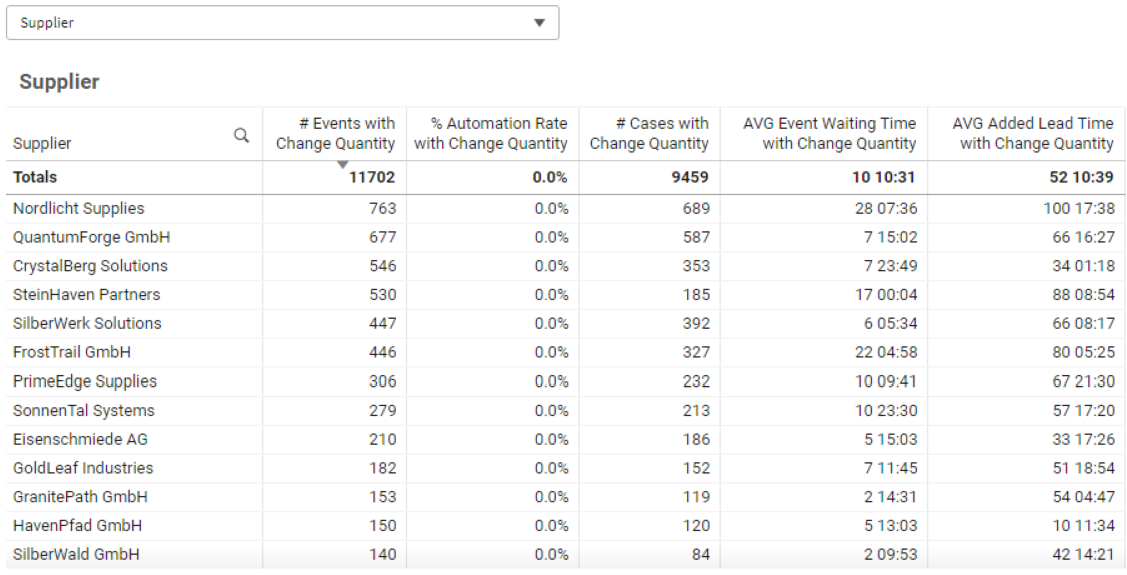
In the bottom left is a table that shows key figures for the dimension that is selected in the dropdown, for instance Supplier. Sort the content based on a specific column by clicking on the header of the column to see which Supplier has the most Change Events (bad), or the highest Automation Rate (good), or the highest Waiting Time (bad). Use these filters to either find bad examples that need to change somehow or to select the best examples to see how they are different and try to copy their success.
💡 Note: Sometimes the combination of multiple factors need to be considered:
- If there is a high number of Change Events, but also a high Automation rate, for instance, then the impact is not so bad because if the change happens automatically then it does not take much time.
- Compare that to Suppliers with a lower number of Change Events but their are mostly done manually, and they are probably going to have a higher Lead Time.
Top 5 Preceding & Succeeding Process Steps​
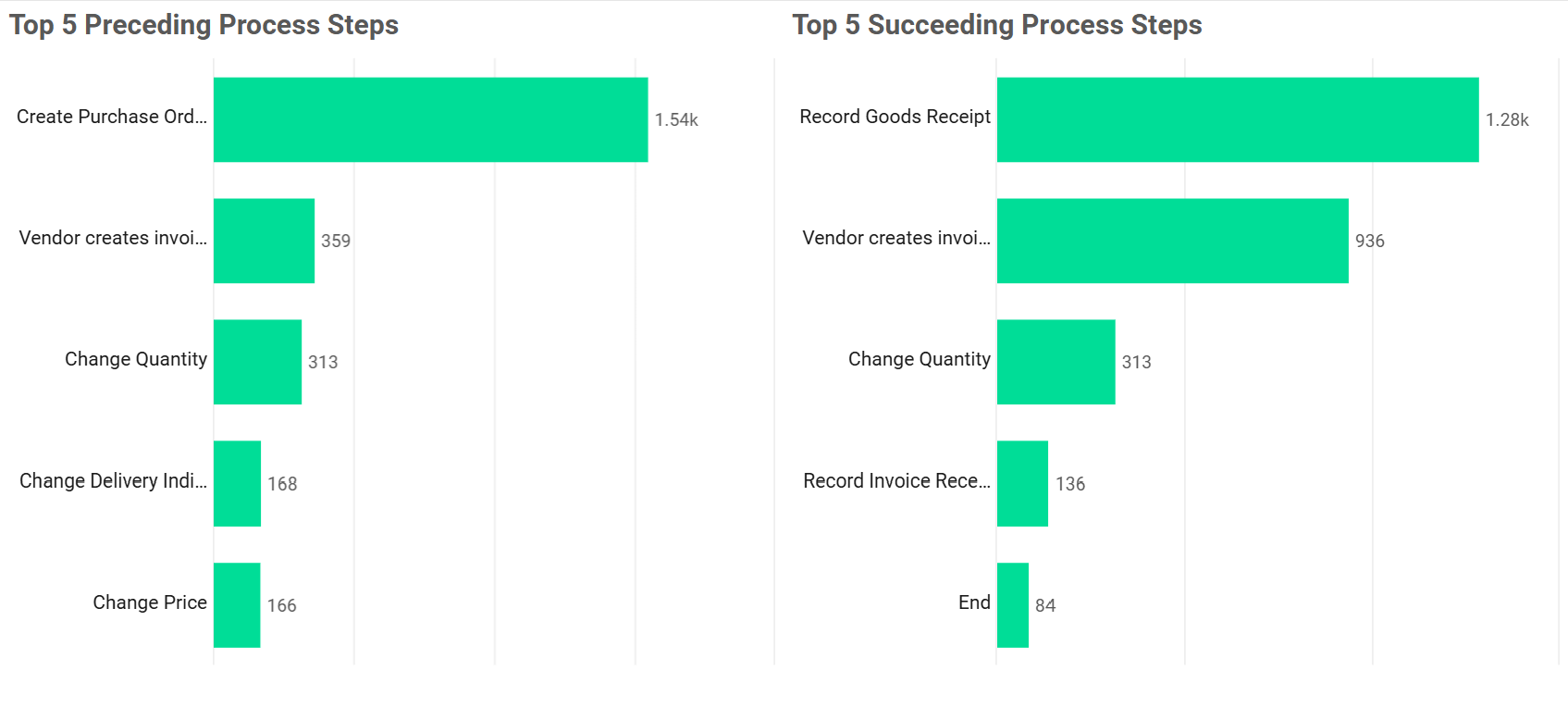
These are used to see if there is a problem in the structure of our process.
If the Price Change usually occurs right after the Purchase Order was created, then this indicates a Master Data problem (the price list needs updating).
If Price Change is usually followed by a Change in Quantity (e.g. price change goes up, quantity goes down) then this is not good for the purchasing process. Prices have to be reliable for the customer to budget how many items they can afford to buy.
Process Variants Inspector​
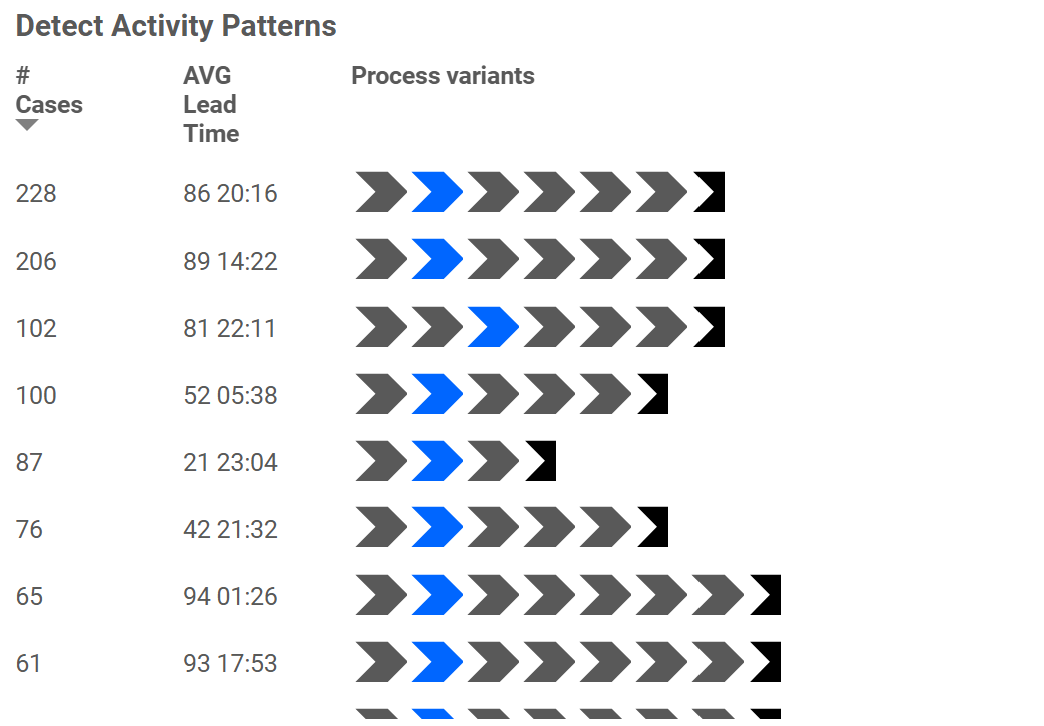
In the bottom right corner you can detect activity patterns. The blue arrows show the selected activity as it occurs in the different process variations. You can see the common process paths that occur before and after the activity. If the Price Change occurs early in the process, it is a structural problem. If it occurs in the middle of the process, it may indicate a communication problem.